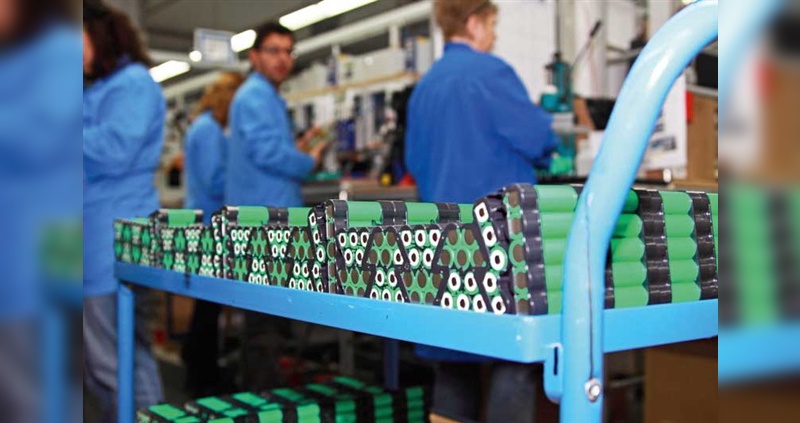
Portrait - Batterien-Montage-Zentrum
Energieriegel fürs Bike
E-Mopeds, Segways und ein 3-D-Drucker, mit dem Prototypen »gedruckt« werden: Schon im Empfangsraum der Batterien-Montage-Zentrum GmbH (BMZ) gibt’s keine Zweifel, worum es hier geht und was das Unternehmen dabei leistet. BMZ ist weltweit ganz vorn mit dabei, wenn es um moderne Elektromobilität geht. Das untermauert der Großbildschirm mit erstaunlichen Umsatzgrafiken des Unternehmens; die wuselige Betriebsamkeit unterstützt das Gefühl, dass hier jemand mit viel Energie die derzeitig vielleicht interessanteste technologische Entwicklung unterstützt und vorantreibt.
Entsprechend selbstbewusst auch die Eigenwahrnehmung im Unternehmen: »Wir machen das Pedelec salonfähig«, sagt Martino Lupo, Leiter der Abteilung E-Bike beim BMZ. »Wir«, das sind mittlerweile 30 Menschen, die sich der Weiterentwicklung der Batterie am E-Bike verschrieben haben und sich um die Kunden, also die E-Bike- und Motoren-Hersteller, kümmern. Mit dem Produkt selbst geht jeder E-Biker und Pedelec-Fahrer selbstverständlich um, ohne zu wissen, was da eigentlich drin ist. Dabei ist das interessant – und gut zu wissen.
Zelle in der Box statt Tiger im Tank
Dass der Energielieferant »Batterie« heißt, kommt nicht von ungefähr. Der wie auch immer geformte Kasten am Bike ist ein Behälter für viele kleine Energieträger, einer ganzen Batterie von so genannten Zellen oder Sekundärzellen. Sie sind wiederaufladbar. Der Gegensatz dazu ist die Primärzelle, eine nicht wiederaufladbare Batterie im umgangssprachlichen Sinn, wie wir sie aus vielen technischen Geräten kennen. Die gebräuchlichste unter den Sekundärzellen ist die 18650: 18 Millimeter Durchmesser, 65 Millimeter lang und mit diesen Maßen fast schon so etwas wie ein Standard. »In fast allen Akkupacks für die Bike-Industrie stecken diese Zellen«, so Lupo. Ihre chemische Zusammensetzung entscheidet über viele Eigenschaften der Batterie, wie Kapazität, Gewicht, Ladedauer oder die Zahl der Ladezyklen. Lithium-Ionen-Zellen sind heute im Qualitätsbereich fast obligatorisch. Noch vor wenigen Jahren setzte man auf die wesentlich schwereren Bleiakkus, später auf Nickel-Cadmium-Varianten.
Mit der Zelle, die BMZ von namhaften Anbietern wie Maxell, Sony, Samsung, Panasonic oder LG bezieht, fängt für das Team um Martino Lupo die Arbeit aber erst an.
Energie im Workflow
»Wir sind alles andere als ein 08/15-Betrieb«, erklärt der drahtige Lupo. »Die Pedelec- oder Motoren-Hersteller kommen mit ihrer Entwicklung zu uns und haben meist schon eine gewisse Vorstellung davon, wie der dazugehörige Batterie-Akku aussehen soll, vielleicht wie er ins Fahrzeug integriert wird, welche Kapazität er haben soll und ähnliches. Wir beraten diese Kunden und übernehmen so viel sie wollen von dieser Aufgabe komplett.« Namhafte Branchenmitglieder geben sich hier die Klinke in die Hand: Ansmann, Cube, Derby Cycle, Gazelle, Heinzmann, Mifa, die ZEG und andere gehören zum Kundenstamm von BMZ.
Die wichtigsten Eckdaten, dann läuft die Maschinerie bei BMZ los: In der Konstruktionsabteilung zeigt Konstrukteur und Designer Pierre Reinhardt, wie am Rechner eine erste Grafik des Produkts entstehen kann. »Schon hier fließen ungeahnt viele Faktoren ein, das geht bis in die Mechanik«, so Reinhardt. Von der Anpassung an den Fahrradrahmen über das Design bis hin zu den Möglichkeiten, einen geeigneten Zell-Halter zu konstruieren – hier muss bereits an alles gedacht werden. Deshalb arbeitet BMZ auch mit vielen Komponenten-Herstellern wie Busch & Müller oder Tubus zusammen. Selbst die Werkzeuge, also die Maschinen, die später für die endgültige Form der Batterie sorgen, werden von BMZ entwickelt.
»Bei uns finden die Kunden echten Pioniergeist«, strahlt Lupo, als wir die Spur der Batterieentwicklung weiter verfolgen, und erzählt von einer ganz speziellen Batterie, die für die neuen Green-Mover-Modelle der ZEG entwickelt wurde. Sowohl die Einpassung in den Rahmen als auch technische Details seien bislang einzigartig. »Einen individuellen Akku für ein E-Bike gibt es schließlich nicht einfach im Regal«, so Lupo. Der wird individuell auf den Kundenwunsch angepasst, wenn der Kunde das will und braucht. Und fast immer geht es um individuelle Lösungen, quasi Custom Made Energy, obwohl BMZ tatsächlich auch einen Standard-Akku für schnell Entschlossene bietet.
Custom Made Energy
Die für den jeweiligen Kundenauftrag nötigen Teile des Produkts werden in der Projektentwicklung definiert. Auch hier sorgt Energie für viel Bewegung. Verschiedene Zulieferer werden abgefragt, ob sie Material nach bestimmten Daten liefern können, es wird eruiert, wer die Werkzeuge liefern könnte und ähnliches. »Es gibt einfach noch sehr wenige Standards in der Branche«, erklärt uns der Leiter der Abteilung, Daniel Maiberger. Wie zum Beweis liegt eine offene Batterie eines Billiganbieters auf dem Tisch, daneben ein Produkt aus dem eigenen Haus.
Im ersten liegen die Zellen in ihrer Box, lediglich in einem Kunststoff-Säckchen eingeschweißt und mit etwas Klebeband fixiert. Das hindert die Zellen nicht daran, bei Erschütterungen in der Batterie durchgeschüttelt zu werden. Die Verbindungen zwischen den Zellpolen sind aus minderwertigem Material. Im BMZ-Produkt erkennt man einen wesentlich aufwendigeren Aufbau: Die Zellen werden oben und unten mit Zellhalter fixiert, verschweißte Hochstrom-Verbinder aus gestanztem Nickelblech sorgen für den optimalen Energiefluss zwischen den Zellen und auf der Oberseite sitzt die Intelligenz der Batterie: die elektronische Steuerung. Sie kontrolliert die vielen sich im Betrieb oft verändernden Daten der Zellen und verhindert Störfälle, die zu Ausfall oder sogar Brand führen können, wie Überladung oder Überhitzung. Der simple »dumme« Akku, wie man ihn hier nennt, birgt hingegen statt einer elektronischen Steuerung lediglich eine handelsübliche Stecksicherung – »die im Zweifelsfall bestenfalls einen Kurzschluss verhindert«, so Lupo. Sicherheit geht vor, das ist auch den Kunden der BMZ-Energiespender klar geworden.
Breite Produktpalette
Apropos Energie: Ein guter E-Bike-Akku ist ein Hybrid, erklärt Lupo, ein perfekter Kompromiss zwischen hoher Stromentnahme und Kapazität. Ganz anders beispielsweise die Batterie für Powertools. Das sind Werkzeuge wie Akkuschrauber oder -Bohrer und Handstaubsauger. Hier ist besonders die kurzzeitige hohe Stromentnahme gefragt. Daneben baut man in Karlstein auch noch Batterien für Automotive-Produkte, medizinische Geräte, Gartentools und, und, und. Bis hin zu Akkus, mit deren Energie in Windkraftanlagen die Rotorblätter gedreht werden, wenn die Windrichtung oder -geschwindigkeit wechselt. Denn auch wenn die Riesen auf dem Feld Ihre eigene Energie herstellen: Auch sie muss gespeichert werden, bevor sie zum Einsatz kommt.
Eindrucksvoll lässt sich der Aufbau der intelligenten BMZ-Batterie fürs E-Bike in der Produktion im Erdgeschoss des Gebäudekomplexes nachvollziehen. Dazu werden wir mit Schutzbrille und -Kittel ausgestattet und außerdem endlich mal richtig geerdet: Eine Streifen elektrisch leitender Folie wird mit der Schuhsohle verklebt, sein Ende in den Schuh gesteckt. So verhindert man, dass bei Berührung von Zellen ein Entladevorgang angeschoben wird (elektrostatische Entladung). Jetzt können wir den Weg von der Zelle zum fertigen »Energieriegel« erkunden. Der »One Piece Flow«-Modus, nach dem hier gearbeitet wird, sorgt für Übersicht und Sicherheit – und bestmögliche Ökonomie.
Nach dem System, das unter anderem durch die Produktionsweise von Toyota bekannt wurde, beherrschen alle Mitarbeiter alle Arbeitsschritte eines gesamten Produktionsprozesses oder einer Produktionslinie und sind für den Gesamtprozess und das daraus resultierende Produkt verantwortlich. Die Einzelteile sind genau abgezählt – bei einem Auftrag von 10.000 Stück findet man an der Produktionslinie kein 10.001tes Bauteil; man braucht also keinen Nachschub an die Linien, kein Überschuss muss abtransportiert werden.
Jedes Produkt hat eine eigene Produktionslinie. Zellen oder Akkupacks, elektronische Steuerung, Zellhalter, Zellverbinder, Verkabelung – all das findet sich sauber in Regalen oder auf Haken am Anfang der Linie; am Ende steht der einbaufertige, noch ungeladene Akku. Gutes Beispiel: Die Linie eines Akkus für einige Gazelle-Pedelecs; fleißige Hände von etwa zehn Mitarbeiterinnen und Mitarbeitern bauen die Gazelle-Batterie in einigen Minuten auf. Sie setzen die Zellen in Zellhalter ein, legen sie in die Gehäuse-Unterschale, setzen Zellverbinder an und verschweißen sie, separat wird die Steuerungselektronik verlötet und aufgesetzt, bis diese schließlich im Gehäuse vergossen wird – also mit einer speziellen wärmeableitenden Vergussmasse aufgefüllt wird. Dieses Material verhärtet nach etwa ein bis drei Stunden, je nach Menge, sodass der Akku beziehungsweise die Elektronik vor Feuchtigkeit, aber auch vor Erschütterung geschützt und abgedichtet ist. Hier kommt es besonders darauf an, die richtige Menge des Vergussmittels einlaufen zu lassen. Zu wenig schafft nicht die erwünschte Sicherheit, zu viel kann die Elektronik zerstören.
Professionelle Vorbilder
Die wichtigste Einrichtung dazu ist die benachbarte Battery University, kurz BU, im selben Gebäudekomplex. Das Prüfinstitut, wie das BMZ unter der Geschäftsführung von Sven Bauer, ist ein unabhängiges Testlabor für Batterien aller Technologien mit einem breiten Servicespektrum rund um Qualitäts- und Sicherheitsprüfungen. Hier werden Batterien für alle Sicherheits-, Transport- und Umweltbelange gemäß der gesetzlichen Vorschriften getestet. »Jede neue Zelle, mit der wir unsere Batterien produzieren«, erklärt Andreas Hasenstab von der BU, »wird hier zunächst geprüft. Sie muss unseren hohen Standards, vor allem in Sachen Sicherheit und Leistungsfähigkeit, genügen.« Aber auch Batterien von Kunden werden hier nach verschiedenen internationalen Normen geprüft. Der internationale Elektromobilitätstrend führt zu neuen Herausforderungen – und dem Wunsch vieler Beteiligter nach neuen Prüfnormen. Die Testnorm EN 62133, die von der Battery University mitentwickelt wurde, definiert als »Europäischer Sicherheitsstandard für Lithium-Ionen-Akkus in Pedelecs und E-Bikes« viele Faktoren, die für die Transportsicherheit und den täglichen Gebrauch einer E-Bike-Batterie nötig sind.
Im Prüflabor der BU wird entsprechend wortwörtlich getestet, was das Zeug hält. Bereits 4.200 Akkupacks wurden hier bislang geprüft, ungefähr 200 Projekte von 1000 Kunden zählt man jährlich. Das geht schon mal richtig gefährlich zu, das erklärt auch, warum es neben dem großen Laborraum einen separaten Testraum hinter Panzerglas gibt. Dort werden Kurzschlüsse bewusst erzeugt, Batterien hohem Druck und Hitze ausgesetzt und vieles mehr. Hasenstab zeigt ein Video eines Tests, bei dem ein Batteriepack in einer Sicherheitskammer mit doppeltem Ladestrom überladen wird: Eine einzelne Zelle explodiert mit gewaltiger Wucht und fängt an zu brennen, es entsteht eine Kettenreaktion in der nach und nach alle Zellen explodieren. »In der Praxis am Ladegerät wäre das eine Katastrophe, selbst unter Laborbedingungen ist ein Batteriebrand kaum zu löschen, da jede weitere Explosion einer Zelle das spezielle Löschmaterial für Metallbrände wieder wegsprengt und durch den Brand enorm hohe Temperaturen entstehen.«
Ganz anders ein Test, der die Situation im Flugzeug simuliert: In einer speziellen Unterdruckkammer wird der Luftdruck auf 115 Millibar abgesenkt, Messgeräte kontrollieren dabei den Zustand der Zellen. Auch Infrarot-Technik kommt zum Einsatz, wenn zum Beispiel beobachtet wird, wie sich eine Batterie beim Entladen thermisch verhält.
Oder der Vibrationstest: Hier werden Batterien an einer tischartigen Basis befestigt. Die gehört zu einer vier Tonnen schweren Maschine, welche Frequenzen erzeugt, wie sie zum Beispiel beim E-Bike-Fahren über schlechtem Untergrund auftreten. So wird der Einfluss von Erschütterungen auf die Batterie untersucht. Aber auch so vermeintlich banale Testanordnungen wie »Nagel dringt in Zelle« gibt es. Untersucht wird einfach alles, was in der Realität auch passieren kann. Endlich einmal eine »Universität«, die sich wirklich bodenständig und praxisorientiert gibt.
Rekreation auch für Rennfahrer
Martino Lupo arbeitet seit einem Jahr beim BMZ. Er bringt seinen Kunden mit Begeisterung nahe, wie viel Energie man in die Entwicklung und Herstellung hochwertiger Akkus stecken sollte, damit die Energie fürs E-Biken auch gut untergebracht ist. Er selbst ist in der Fahrradbranche kein Unbekannter: Leidenschaftlicher Rennradfahrer, zwei Jahre Profi-Rennsporterfahrung und lange Zeit Mitarbeiter bei Fahrradhersteller Hercules. Fährt denn so jemand E-Bike? »Ja, klar! Wenn ich jetzt nach dem Job nach Hause komme, ist das das Beste, was ich zum Entspannen machen kann: Bei Lust und Laune mich auspowern, aber genauso gut kann ich völlig sorgenfrei und entspannt mit wenig Anstrengung einfach die Natur genießen«, freut sich Lupo. Und zeigt damit fast beispielhaft, wie breit das Nutzerspektrum von Pedelecs und E-Bikes angelegt ist. Das spricht dafür, dass es in Karlstein in Zukunft noch mehr zu tun geben wird.
Verknüpfte Firmen abonnieren
für unsere Abonnenten sichtbar.