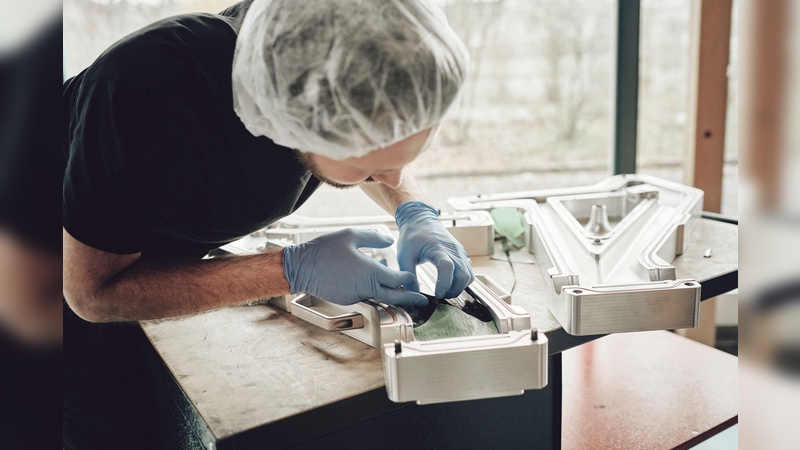
Industrie - Produktion in Europa
Zurück nach Europa
In den 1990er-Jahren gab Europa einen Großteil seiner Stahlrahmenproduktion zugunsten von Alurahmenimporten aus Fernost auf und die meisten Markenhersteller fokussierten auf ihre hiesigen Entwicklungsabteilungen. So kam es, dass heute rund 90 Prozent aller hochwertigen, in Serie gefertigten Fahrradrahmen aus Asien kommen.
Vor allem Taiwan und die Volksrepublik China gehören zu den bedeutendsten Produktionsländern für die europäische Fahrradbranche, und das nicht nur für Rahmen aus Aluminium, sondern auch für solche aus Carbon. Dies auch, weil der Bau der heute überwiegenden Duroplast-Carbonrahmen mit viel Handarbeit verbunden ist und die Arbeitskosten in China damals tief waren. Seit dem WTO-Beitritt 2001 hat sich das Land aber wirtschaftlich rasant entwickelt und die dortigen Löhne sind stark gestiegen. Dazu kommt, dass die jüngsten Handelsstreitigkeiten zwischen dem Westen und China zu Strafzöllen für chinesische Erzeugnisse beziehungsweise zur Verlängerung von bestehenden Antidumpingzöllen geführt haben. In Taiwan hingegen hat die Industrie Schwierigkeiten, Fachkräfte zu finden. 2017 wurde ein strikteres Arbeitsgesetz eingeführt, das taiwanischen Unternehmen verbietet, seine Angestellten mehr als 40 Stunden pro Woche arbeiten zu lassen.
Um Kosten zu senken, mehr Kapazitäten aufzubauen und die Zölle zu umgehen, verlagerten in der Folge viele taiwanische Rahmenbauer ihre Fabriken nach Vietnam und Kambodscha. Das ist zwar kostengünstiger, bringt aber auch Nachteile mit sich – allen voran die langen Lieferfristen. Denn bis die Abläufe in diesen Fabriken reibungslos funktionieren, vergeht Zeit. Zeit, die die Fahrradindustrie mit ihren immer kürzer werdenden Produktzyklen nicht hat. Gerade in Anbetracht der rasanten technischen Entwicklung des E-Bikes und der steigender Nachfrage danach wurde dies für die europäische Velobranche zum Problem. Stichwort: Verfügbarkeit.
Europäische »Bike Valleys«
Um dieses Problems Herr zu werden, arbeitet die europäische Fahrradbranche seit mehreren Jahren an marktnahen Serienrahmenproduktionen, die nun durch automatisierte Fertigungsverfahren ermöglicht und zunehmend Realität werden. Um Synergieeffekte zu nutzen sowie flexibler und schneller produzieren zu können, schließen sich Unternehmen in verschiedenen Ländern zu sogenannten »Bike Valleys« zusammen. Eines davon befindet sich im portugiesischen Agueda, einer Region, in der bereits seit mehr als 90 Jahren Fahrräder hergestellt werden. Die Initiatoren dahinter sind die portugiesischen Komponentenanbieter Ciclo Fapril, Miranda und Rodi, die 2015 gemeinsam die Triangle’s Cycling Equipments S.A. gegründet haben. Die drei Unternehmen haben das Projekt mit rund 15 Millionen Euro Unterstützungsgeldern der EU aufgezogen und die weltweit erste komplett automatisierte Alurahmenproduktion realisiert.
Unter anderem ermöglichen dies 18 Schweißroboter von einem der Auto- branche nahestehenden Maschinenbauspezialisten aus Deutschland. So sollen die Lohnkostenvorteile der konkurrierenden Rahmenbauer in Fernost wettgemacht werden. Damit die Roboter ihre Arbeit verrichten können, müssen die Rahmenrohre präzise vorbereitet sein. Dafür ist die Triangle’s-Fabrik mit Apparaten des Fahrradbaumaschinen-Spezialisten Bike Machinery aus Italien ausgestattet. Diese schneiden, formen und präparieren die Rohre exakt und sorgen dafür, dass keine Toleranzen auftreten.
Dank der voll automatisierten Produktion benötigt Triangle’s weniger als fünf Minuten, um einen Alurahmen herzustellen, egal, ob für ein Citybike, ein vollgefedertes Mountain- oder ein E-Bike. Laut eigenen Angaben soll die Fabrik eine Kapazität von rund 450.000 Rahmen pro Jahr erreichen.
Mittlerweile investieren auch taiwanische Rahmenbauspezialisten in Fa-briken im »Portugal Bike Valley«. Darunter William Deng oder Fritz Jou Manufacturing, der unter anderem testweise Räder für Flyer assemblierte. Laut eigenen Angaben wurden im »Bike Valley« in Portugal 2018 bereits mehr als zwei Millionen Rahmen hergestellt. So erstaunt es nicht, dass immer mehr Fahrradmarken weniger Rahmen in Asien fertigen lassen und stattdessen verstärkt in Portugal produzieren, um den europäischen Markt zu bedienen. Dazu gehören etwa Orbea oder Riese & Müller. Die Vorteile liegen auf der Hand: mehr Kontrolle über die Fertigungsmethoden und die Arbeitsbedingungen, mehr Flexibilität, um rasch auf Marktveränderungen reagieren zu können, sowie geringere Kosten für den Transport der in Europa abgesetzten Produkte. Die Coronakrise unterstreicht all dies zusätzlich. Außerdem ist die marktnahe Produktion auch umweltfreundlicher. Schließlich wird die Ware entweder auf mit Schweröl betriebenen Frachtern oder per Flugzeug von Asien nach Europa transportiert.
Diese Innovation ist intelligent und grün.Ton AnbeekCEO Accell Group
Vollautomatische Carbonrahmenproduktion
Derzeit wachsen zwei weitere europäische »Bike Valleys« heran. Das eine in Osteuropa (Bulgarien, Polen, Rumänien, Slowakei und Ungarn), das andere im belgischen Flandern. Beide verfolgen ein ähnliches Ziel wie die portugiesischen Unternehmungen: eine marktnahe Serienfertigung hochwertiger Rahmen. Dass dies dank Industrie 4.0 auch für Carbonrahmen möglich ist, beweist das im belgischen Leuven ansässige Unternehmen Rein4ced. 2017 hat es einen neuen Verbundwerkstoff sowie ein Verfahren entwickelt, um vollautomatisch HighEnd-Carbonrahmen herzustellen.
Die Produktion von Duroplast-Carbonrahmen, die heute die Norm darstellt, ist in den letzten Jahren nahezu unverändert geblieben: Zugeschnittene Fasergeflechte werden in einer Form Schicht für Schicht von Hand gelegt, verklebt und in einem Ofen zu einem Ganzen geformt. Diese Methode ist nicht nur zeitaufwendig, sondern auch fehleranfällig. So werden zwischen 20 und 40 Arbeitsstunden benötigt, um einen Rahmen zu fertigen. Toleranzen bei Stabilität und Gewicht inklusive.
»Wir wollten dies mit einer neuen automatisierten Produktionsmethode ändern«, sagt Rein4ced-CEO Michaël Callens. Seine Rahmen bestehen aus thermoplastischen Carbonschichten und sind mit eigens entwickelten, hauchdünnen Stahlfasern verstärkt. Bei Rein4ced beginnt der Produktionsprozess wie folgt: Roboter verlegen die Fasermatten automatisch, bevor diese erwärmt und in einer leistungsstarken Presse zu verschiedenen Bauteilen geformt werden. Diese werden miteinander zu einem Rahmen verbunden. Weil Rein4ced Thermoplast-Carbon verwendet, das beliebig oft erhitzt und abgekühlt werden kann, muss nicht der gesamte Rahmen auf einmal gefertigt werden. »Durch die kürzere Taktzeit pro Bauteil können wir einfacher skalieren und die Produktionsgeschwindigkeit erhöhen«, erläutert Callens.
Laut Rein4ced zeigen wissenschaftliche Tests, dass die Schlagzähigkeit des neuen, verstärkten Verbundmaterials Feather, viel höher ist als die des aktuellen Kohlenstoffmaterials. Dies erreicht das Unternehmen durch die Verstärkung der Carbonfasern mit den besagten hauchdünnen Stahlfasern. Trotz dieser Fasern soll das Gewicht nicht höher ausfallen als bei heutigen High-End-Duroplast-Carbonrahmen.
Als erster großer Kunde will die Accell Group von signifikanten Vorteilen in der Logistik und Nachhaltigkeit sowie von erhöhter Flexibilität und Effizienz der Lieferkette profitieren. Dazu sagt CEO Ton Anbeek: »Diese Zusammenarbeit entspricht unserer globalen Innovationsstrategie und dem Bestreben, unseren CO2-Fußabdruck weiter zu reduzieren. Die neue ›Feather‹-Technologie verbessert die Stabilität und Haltbarkeit der Fahrradrahmen. Anders ausgedrückt: Diese Innovation ist intelligent und grün.« Laut Rein4ced bietet die automatisierte Produktionsstätte in Leuven aktuell eine jährliche Produktionskapazität von bis zu 20.000 Rahmen. Und die Belgier bauen weiter aus: Im Mai wurde im Engineering und in der Produktion personell aufgestockt.
Verknüpfte Firmen abonnieren
für unsere Abonnenten sichtbar.