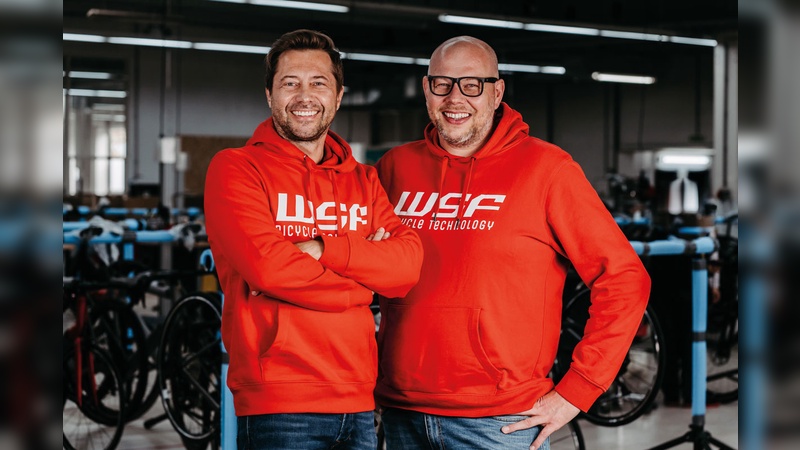
Industrie - Montagebetrieb WSF
Perfektion aus Notwendigkeit
Wenn man mit den beiden Gründern Alexander Schnöll und Roland Wallmannsberger spricht, dann wird sehr schnell klar, dass man es mit zwei tatkräftigen, fähigen, offenen und damit nicht zuletzt sympathischen Österreichern zu tun hat. Im September 2020 haben die beiden in den Räumen einer ehemaligen Druckerei ihren Montagebetrieb gegründet, also zu einem Zeitpunkt, als allen in der Branche gerade klar wurde, dass die nächste Zeit ausgesprochen hart werden würde. Optimal war der Zeitpunkt für die Gründung damit keineswegs, wie Schnöll feststellt: »Wir wären gerne ein Jahr früher gestartet.«
WSF steht für die Initialen der Gründer, wobei das »F« sich nicht rechtzeitig von seinem Job in der Automobilbranche lösen konnte. Als Namensgeber ist er aber dennoch verewigt. »Er ist ein sehr guter Arbeitskollege und mittlerweile sehr guter Freund von uns, aber immer noch Berater in der Automobilindustrie«, erklärt Wallmannsberger. »Das heißt nicht, dass er nicht doch irgendwann noch dazustößt.« Damit es zur Gründung der WSF Bicycle Technology GmbH im österreichischen Regnau kommen konnte, musste zuerst einiges zusammenkommen.
»Die Idee ist entstanden aus einem gemeinsamen Beratungsprojekt für einen deutschen Fahrradhersteller«, erläutert Wallmannsberger. Gut zwei Jahre lang hatten die beiden dort die Gelegenheit, die Eigenheiten der Fahrradproduktion im Detail kennenzulernen. »Bevor wir dort angefangen haben, waren wir komplett blauäugig. Wir haben nichts über die Branche gewusst.« Davor waren beide in der Automobilwelt in verschiedenen Beratungsfunktionen tätig und gleichzeitig schon lange befreundet. Überhaupt haben beide sehr illustre Lebensläufe vorzuzeigen. Wallmannsberger etwa arbeitete zuvor als Maschinenschlosser-Meister, Lkw-Fahrer, Türsteher, Einkaufsleiter und manches mehr, bis er schließlich im Automobilsektor landete, ein MBA-Studium absolvierte und sich schließlich selbstständig machte. Schnöll hat unter anderem ein Studium »Produktion und Management« für die kommende Aufgabe vorbereitet. Er schlug eine Laufbahn im gehobenen Management in der Automobilbranche aus. An diesem Punkt hatten die beiden privat und beruflich schon viele Anknüpfungspunkte, die dann letztlich zur Gründung von WSF führten. Doch der Weg dahin war so eigentlich nicht beabsichtigt.
WSF steht übrigens nicht wirklich für »whatsefuck«, sondern die Initialen der Gründer.
Schnöll führt aus: »Wir wurden für ein Projekt für einen Hersteller geholt, bei dem sich so viele notwendige Veränderungen ergaben, dass es immer größer wurde. Unter anderem ging es dabei auch um die bestehenden Montage-Dienstleister. Unsere Aufgabe war, sie und andere zu untersuchen und zu schauen, welche zu uns passen würden.« Für die beiden, die aus dem Automotive-Bereich kommen, war dann schnell klar, dass die Art und Weise, wie da gearbeitet wurde, sehr fehleranfällig war und nicht zu vereinen mit den Standards, die sie in der Automobilwelt verinnerlicht hatten. »Ich war schließlich so gefrustet«, erinnert sich Wallmannsberger, »dass ich eines Abends gesagt habe: ›Wir machen das einfach selbst.‹« Letztlich sei dies die einzige Möglichkeit gewesen, aus dem bestehenden Kreislauf auszubrechen. »Du wirst als Berater für viel Geld geholt, um Veränderungen zu bewirken, aber schaffst es dann nicht. Aber nicht wegen deiner eigenen Unfähigkeit oder deines Teams oder des Herstellers, sondern weil Hürden im Produktionsprozess bestehen, die sich nicht beseitigen lassen. Am Ende des Abends waren drei Flaschen Wein getrunken und unsere Firma vor dem geistigen Auge mehr oder weniger fertig.«
»Die Fahrradindustrie ist die mit Abstand fürchterlichste Industrie, die ich jemals in meinem Leben gesehen habe.«
Roland Wallmannsberger, WSF
Danach haben sich die beiden aber doch noch zwei weitere Wochen Zeit genommen und an der Idee gefeilt, bevor sie tatsächlich an die Umsetzung gingen. Das Projekt beim Hersteller ging bereits seinem Ende zu. Entsprechend schnell ging die Arbeit am Businessplan anschließend voran und durch Corona waren die beiden ohnehin »einkaserniert«. »Wir haben Corona gar nicht richtig mitbekommen und am Unternehmen gearbeitet«, ergänzt Schnöll. »Wir wollten einen sauberen Businessplan schreiben, der nicht nur Zahlenspielereien beinhaltet, sondern eine Branchenanalyse. Zudem haben wir potenzielle Kunden identifiziert und sie gefragt, ob sie unsere Dienstleistung überhaupt brauchen.«
Die beiden nehmen kein Blatt vor den Mund, wenn sie die Situation in der Fahrradproduktion beschreiben sollen, wie sie ihnen begegnet ist: »Ich sage das jedem, ob er es hören will oder nicht: Die Fahrradindustrie ist die mit Abstand fürchterlichste Industrie, die ich jemals in meinem Leben gesehen habe. Was sie kann, ist ein geiles Fahrrad hinstellen.« Aber diese Begeisterung fürs Produkt reiche nicht aus und der Weg dahin sei oft fragwürdig. Zu oft habe er Entscheidungen gesehen, die betriebswirtschaftlich unprofessionell waren. »Da sind wir einfach komplett anders.« Statt um Fahrradbegeisterung gehe es bei der Montage um klare Vorgaben und definierte Arbeitsschritte. So habe man nur sehr wenige Mitarbeiter mit Fahrraderfahrung, die trotzdem genau wissen, was sie tun. »Wir haben ein paar Radverrückte, die braucht man, keine Frage«, erklärt Wallmannsberger, »ohne die geht es nicht. Davon bin ich überzeugt.« Aber willkürliche Planänderungen und sprunghafte Entscheidungen könne man nicht gebrauchen. Stattdessen legen die beiden Gründer größten Wert auf eine exakte Planung der Produktion.
Doch was unterscheidet denn nun die Fahrradmontage bei WSF von der bei einem beliebigen anderen Betrieb? »Wir haben verschiedene Montagebetriebe in Deutschland, Polen, Tschechien, Taiwan gesehen. In der Regel wurden Teilelisten verschickt, die oft unvollständig waren. Am Ende des Prozesses kamen dann Räder, wo man bei einhundert montierten Rädern einhundert Reklamationen hat«, beschreibt Wallmannsberger die Ausgangslage. »Wir haben uns dann gefragt, woran das liegt. Oft lag es daran, dass der Fertiger gar nicht die nötigen Informationen bekommen hat, um seine Aufgabe zu erfüllen. Das war durchgängig der Fall in der Branche. Das sind so grundlegende Dinge, die es im Automobilbereich so nie geben würde. Da gibt es eine Übergabe, sodass jeder weiß, was als Nächstes zu tun ist. Das zieht sich durch bis zur Verpackung.« Dass es an diesen grundlegenden Sachen fehlt, beobachtet Wallmannsberger nach wie vor, etwa wenn ein Kunde Material für einen Musterbau zusendet.
Die Produktion im österreichischen Regau ist präzise organisiert. Detaillierte Bauanleitungen für die Monteure sorgen dafür, dass gleichbleibende Qualität sichergestellt wird.
Es fehlten oft viele Teile, sei es der Schrumpfschlauch, ein Kabel oder andere Kleinteile. »Da merkt man, wie groß die Diskrepanz ist. Genau da muss man ansetzen.«
Bei WSF wird zuerst ein Musterbike aufgebaut und alle Schritte genau analysiert. Dann wird den Kunden ein Angebot unterbreitet. Anschließend wird eine Nullserie gebaut, aus der alle einzelnen Bestandteile exakt aufgeführt und alle Arbeitsschritte samt Drehmomentangaben dokumentiert sind. Zwei Mitarbeiter kümmern sich um nichts anderes, als Aufbaudokumentationen zu erstellen für die Facharbeiter und -arbeiterinnen am Band, sodass das Ergebnis heute, morgen und in drei Jahren immer exakt reproduziert werden kann.
Definierte Prozesse sorgen für hohe Montagequalität
»Bei uns ist bis zur kleinsten Hülse oder Schraube alles in der Stückliste dokumentiert«, erklärt Schnöll. »Zudem sind alle Bestandteile bis ins Detail spezifiziert«. Wenn etwa ein Kunde wünscht, etwas mit einem Kabelbinder zu befestigen, dann werde zurückgefragt, welcher genau es sein soll. So bleiben keinerlei Unklarheiten übrig, der Prozess der Produktion wird von Stopfen über Unterlegscheibe bis zum Stecker exakt definiert und ausformuliert. »Glaubt jemand ernsthaft, dass bei BMW jemand sagt: ›Jetzt nehmt irgendeinen Kabelbinder her‹?«, fragt Wallmannsberger. »Da wird genau definiert, wie lichtbeständig er sein muss, welche Größe er hat und alles andere. All diese Dinge sind in der Fahrradbranche noch gar nicht vorhanden.«
»Die Perfektion kommt ja nicht aus purem Idealismus, sondern aus einer Notwendigkeit, um später wirtschaftlich und effizient bauen zu können. Wir sind nicht in einem Billiglohnland, bei uns müssen alle Fragen vorab beantwortet sein, denn später in der Produktion zählt jede Minute«, verdeutlicht Schnöll. Wenn man das nicht tut, komme man schnell ins Stocken. Darum stelle man den Herstellern nach dem Musterbau meist viele Dutzend Fragen, über die sich selbst gestandene Produktmanager oft noch nie Gedanken gemacht haben.
Der Anspruch ist, am Ende eine Vormontagequalität zu liefern, die über jeden Zweifel erhaben ist. »Es ist doch traurig, einem Händler zusätzliche Arbeit zu bereiten, weil man schlechte Qualität liefert«, sagt Wallmannsberger Es gehe dabei nicht einmal darum, den Markenherstellern einen Gefallen zu tun, es sei schlicht das notwendige Ergebnis in diesem strukturierten Arbeitsprozess. »Es war nie unser Ansatz, Preise wie in Tschechien möglich zu machen. Billigfahrräder können und wollen wir hier nicht machen. Bei den mittel- und höherpreisigen Fahrrädern muss aber die Qualität passen«, sagt Schnöll.
Mit dem eigenen hohen Anspruch legte man mehr oder weniger eine Art Traumstart hin: Im Juli 2021 haben die beiden eine Mail an die Fahrradhersteller verschickt. »Eine furchtbar schlechte Präsentation« wurde laut Wallmannsberger an insgesamt 200 Unternehmen verschickt. Die erste Antwort kam bereits 26 Minuten später. »Insgesamt haben sich 130 Unternehmen bei uns gemeldet«. Das Interesse zu diesem Zeitpunkt war überwältigend, »die Delegationen der Unternehmen wollten gleich vorbeikommen«, erinnert sich Schnöll. Im gleichen Monat kam dann der erste Auftrag, im September 2021 liefen die ersten Räder vom Band. Vom Start weg hat man die knapp 7000 Quadratmeter verfügbare Fläche in Regnau gebraucht und hätte inzwischen sogar schon Bedarf nach mehr. Allerdings geben die Gründer unumwunden zu, dass die Prozesse zum Start noch gar nicht so funktioniert haben, wie sie es sich vorgestellt haben. Auch hier gab es eine Lernkurve. Heute hat man diese Dinge im Griff. Die Skalierung nach oben läuft derzeit kontinuierlich, auch wenn es nicht so schnell geht, wie es sich der Markt derzeit wohl wünscht. Es gibt immer noch viele Dinge, an denen das Team arbeitet, etwa am ERP-System. Aber eines ist offensichtlich: Die beiden haben einen Nerv der Branche getroffen. Fahrräder, die in Regau montiert wurden, dürfte man demnächst häufiger auf der Straße fahren sehen. //
Verknüpfte Firmen abonnieren
für unsere Abonnenten sichtbar.