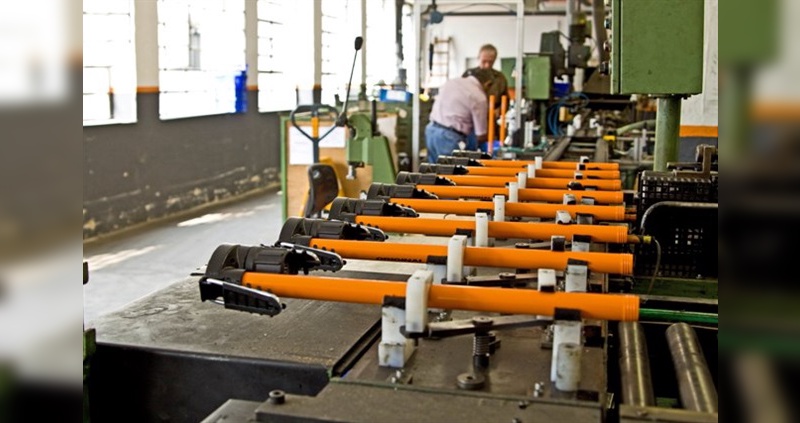
PUMPEN WIE EIN WELTMEISTER
SKS IM PORTRAIT: SAUERLÄNDISCHER KUNSTSTOFF-SUPERMAN
positiven Überraschungen erlebt. Die erste beschert bereits das Navigationsgerät: Es führt direkt in die Innenstadt des Orts mit knapp 30.000 Einwohnern. Das Unternehmen sitzt seit 1921 mitten in Sundern. Wenige Meter vom Rathaus entfernt wehen drei Flaggen, die dem Rad-Branchenkennern den Weg zur Welt von Luftpumpe und Schutzblech weisen. Eine ungewöhnliche Lage für ein Unternehmen, das auf satten 36.000 Quadratmetern – reine Produktionsfläche – Produkte aus Kunststoff produziert. Rund 270 Leute arbeiten allein hier in Sundern für SKS. Aber der Reihe nach.
DIE GANZE RAD-WELT IN ORANGE
Schmal, dreistöckig und hoher Glasanteil: So präsentiert sich die Fassade der Unternehmens-Gruppe, zu der neben SKS Metaplast auch Blomus (elegante Wohn-Accessoires) und Schött (Aluminium-Druckguss Automotive) gehören.
Hell und sehr modern geht’s innen weiter. Glas ersetzt Bürowände, Durchblick überall. Das ist nicht nur räumlich gemeint: „Seit dem 1. Januar 2009 arbeiten wir im Direktvertrieb, und dadurch ändert sich viel in puncto Öffentlichkeitsarbeit“, so Produktmanager Sebastian Wedhorn. Seitdem wird versucht, die Marke SKS metaplast – die Abkürzung setzt sich aus den Anfangsbuchstaben des Gründers Scheffer Klute und des Standorts Sundern zusammen – besser ins Bewusstsein der Öffentlichkeit und der Fachhändler zu bringen. Und zwar mit System. Da wird beispielsweise eine über 800 Quadratmeter große Montagehalle zum Showroom mit kombinierter Lounge und flexiblen Besprechungs- und Tagungs-Räumen umgebaut.Das erst vor Kurzem fertiggestellte Ergebnis, „Orange World“ genannt, kann sich mit seinen kontrastierenden Anklängen an die vergangene Zeit der klassischen Manufaktur sehen lassen. Alle Produkte der Firma sind ausgestellt, und auch die Geschichte wird gezeigt. Den Original-Musterkoffer des früheren Geschäftsführers Willhelm Blome senior etwa, voll mit Handpumpen aus den 60er Jahren. Die Produkte prägen das Ambiente. Die flexiblen Trennwände zeigen vor allem Explosionszeichnungen von Luftpumpen.
Die Feuerprobe der ersten Händlerschulungen hat Orange World bereits bestanden. Dabei setzte man auf Synergie: Conti und Busch & Müller trafen sich für gemeinsame Händlerschulungen mit SKS. Aber auch im Event-Bereich tritt SKS gut sichtbar auf, sei es mit dem SKS-Bike-Marathon, der auf dem Firmengelände gestartet wird, dem SKS-Rohloff-MTB-Nordhessen-Cup oder dem Ruhrtalradwegfest in Menden.
LUFTPUPMEN MIT AUTOMOTIVE-ANSPRUCH
Die Bauteile für schier unglaubliche 50.000 Luftpumpen täglich werden in der firmeneigenen Spritzerei produziert. Dabei ist die Pumpe ein wesentlich komplexeres Produkt, als man gemeinhin glaubt, wie sich schnell zeigt: In der Entwicklungsabteilung von Sven Kordes entstehen alle Pumpen oder Veränderungen an vorhandenen Produkten zunächst am Rechner. Ist der erste Funktions-Entwurf fertig, übernimmt die Design-Agentur, mit der SKS zusammenarbeitet. Mit ihr zusammen wird ein Prototyp erarbeitet, der zunächst getestet wird. Klappt das Ganze, treten die Werkzeugmacher auf den Plan: „98 Prozent dessen, was das Haus verlässt, wird auch hier im Sauerland produziert“, so Wedhorn. SKS fertigt also fast alles selbst; auch die Spritzguss-Werkzeuge für die Produkte! Eine eigene große Abteilung ist mit der Entwicklung der Werkzeuge, also der Spritzgussformen, beschäftigt. „Etwa 16 Wochen dauert dieser Vorgang im Schnitt, bis die Werkzeuge fertig sind und die ersten Vorserien-Pumpen entstehen. Luftpumpen sind sehr komplexe Produkte“, erklärt Chefentwickler Kordes, „die Fertigungstoleranzen sind hier sehr gering!“ Dabei kommt dem Unternehmen die Erfahrung aus dem Automotive-Bereich zugute. Hier herrschen bekanntlich immer noch wesentlich höhere Anforderungen als in der Fahrradbranche. Wer diesen in Entwicklung und Fertigung genügt, steht gut da. Da lohnt es sich, volle 90.000 Euro in die Entwicklung einer neuen Pumpe zu investieren, die im Fachhandel dann vielleicht um die 15 Euro kostet.
Wie komplex die Herstellung der stählernen Spritzguss-Blöcke ist, wird klar, wenn man die vielfältigen Formen der Einzelteile von Pumpen sieht – und die entsprechenden Formen nebst Einspritzkanälen und weiteren Details im Block. Dazu kommen weitere Schwierigkeiten: Kunststoffe verschiedener Farbe können unterschiedliche Materialeigenschaften haben. Das macht die Fertigung nicht einfacher. Trotzdem: In der Spritzerei stehen 45 Spritz-Monster nebeneinander und spritzen, von Mitarbeitern überwacht, emsig vor sich hin – schließlich müssen die Zahlen erreicht werden.
In der nächsten Halle werkeln riesige bizarre Maschinen: Sie montieren, teils hinter Gitter, vollautomatisch Pumpen, die nach der Qualitätskontrolle direkt in Verpackungen wandern.
Ausschließlich per Hand montiert wird ein SKS-Kultobjekt: der Rennkompressor. Die berühmte Standpumpe, schon seit knapp 40 Jahren fast unverändert produziert, ist der absolute Renner unter den Pumpen aus Sundern. Wen wundert’s? Der – natürlich in SKS-Orange gehaltene – Druckmacher schafft maximal 16 bar, ist als absolut zuverlässig bekannt und dementsprechend nicht nur in den meisten Rennställen der Welt zu finden.
UNHEILIG’S BLECHLE
Weit weniger komplex als die Pumpenfertigung zeigt sich die Fertigung – die Extrusion – der Schutzbleche, pardon: Radschützer. „Das ist schließlich kein Blech!“, sagte Wilhelm Blome sen. 1985 und erhob damit den Begriff „Radschützer“ zum festen Terminus bei SKS. Auch diese Teile klotzen mit dicken Zahlen. Etwa 10.000 sind es pro Tag, mehr als die Hälfte geht in den Export. Dabei stieg man erst 1983 ins Geschäft ein – allerdings mit einem lauten Knall: Damals wurde der englische Traditionshersteller Bluemels übernommen, ein Name, der heute noch für eine klassische SKS-Radschützer-Serie steht. Auch die Übernahme von ESGE brachte das Unternehmen weiter. 1988 startete man in Sundern die damals modernste Fertigung. Vereinfacht gesprochen wird ein weniger als einen Millimeter dünne Alu-Folie über Laufrollen und dabei durch heißen, flüssigen Kunststoff gezogen, der sich dabei rundum anheftet. Kommt das Band so ummantelt aus dem Kunststoffbad, wird es abgekühlt und mit Spannung über ein Rad gezogen, wobei der Radschutz seine horizontale und vertikale Krümmung erhält. Im Anschluss wird auf die jeweils richtige Länge abgeschnitten, und in den nächsten Arbeitsschritten erhalten die „Bleche“ ihre Spoiler, Kantenschoner und Befestigungselemente. Im Vergleich zur Pumpenfertigung also ein leichtes Spiel. Durch verschiedene Kunststoffe und Alufolie kann das Design stark individualisiert werden. „Etwa 80 verschiedene Farben sind zum Beispiel möglich“, so Wedhorn, „wir stellen insgesamt etwa 1.200 verschiedene Variationen Radschützer her. Jeder Radhersteller bekommt seine Wünsche erfüllt. Standard gibt’s fast nur für den After Market.“ Also zum Beispiel für die Leute, die im Fachhandel fest montierbare Radschützer für ihr Crossrad kaufen.
PERSPEKTIVE: ERFOLG
Alle Gesprächspartner bei SKS strahlen eine gelassene Zufriedenheit aus. Da muss was dran sein. „Bis auf das Krisenjahr 2009 haben wir jährlich ein deutliches Umsatz-Plus gemacht“, lächelt Michael Beste, neben Willo Blome Geschäftsführer von SKS Metaplast in Sundern. „Wir wollen nicht krampfhaft nach vorn preschen, planen aber ein gesundes Wachstum von zehn bis 15 Prozent jährlich“, erklärt der für einen Konzernchef enorm leger auftretende Geschäftsführer selbstbewusst. Zu den guten Zahlen kommen schließlich auch eine um vor Jahren um Mini-Tools und vor Kurzem um Satteltaschen erweiterte Produktrange.
Wer jetzt denkt, da platzt der Standort Sundern aus allen Nähten, liegt falsch. Gerade konnte das Unternehmen die Halle eines Nachbarn am westlichen Ende des ohnehin schon gewaltigen Komplexes aufkaufen. „Da geht noch was“, freut sich Beste, „wir haben traditionell einen starken Bezug zur Stadt, und das wird auch so bleiben.“ Und „Made in Germany“ stand ohnehin noch nie zur Debatte; umso weniger heute, da dieses Versprechen Gold wert ist.
Lediglich die Verkehrsinfrastruktur spricht nicht rundum für den Sauerland-Standort Sundern, denn egal aus welcher Richtung man kommt, zumindest die letzten 20 Kilometer zum SKS-Werk sind gewundene kleine Sträßchen; für den LKW-Transport zeitintensive Transportwege. Aber man kann schließlich nicht alles haben …
Verknüpfte Firmen abonnieren
für unsere Abonnenten sichtbar.